Canada Post Corporation - Rosedale Letter Carrier Depot
Certifications & Awards
Project Team
- Architect: Omicron
- Mechanical : Omicron
- Electrical : Omicron
- Civil : McElhanney Consulting Services Ltd.
- Landscape Architect : Matrix Landscape Architecture
- LEED Consulting : Omicron & Light House
- Contractor : Dawson Wallace Contstruction Ltd.
- Remediation Contractor : Tervita Corp.
- Environmental Agency : PHH Arc Environmental
- Owner : Canada Post
- Commissioning Authority : SNC Lavalin O&M
Green Building Audio
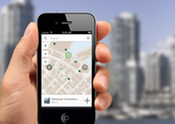
Our audio tours qualify.
Get one today!
Canada Post Rosedale Letter Carrier Depot - Joanne Sawatzky, Light House
Summary
The Canada Post Corporation’s Rosedale Letter Carrier Depot in Edmonton, Alberta was designed and constructed as part of Canada Post’s ‘transformation program’, modernizing postal facilities, equipment and processes in order to improve efficiency, productivity, and employee safety. The 2,657 square meter (28,600 square foot) light industrial office and warehouse in Edmonton’s Rosedale region is used as a sorting and consolidation center for large quantities of mail for delivery and distribution, and built to facilitate increased demands as one of the largest distribution centres in Edmonton.
The project has targeted certification via the Canada Green Building Council’s Leadership in Energy and Environmental Design (LEED) Rating System.
The building is occupied by 69 full time equivalent employees, and served by ancillary spaces such as locker rooms, showers and lunchrooms.
As this project is owner-managed and will be maintained as a long term asset, the owner has invested in better infrastructure up-front to improve employee comfort and reduce maintenance costs.
Sustainable Sites
Alternative Transportation
The Letter Carrier Depot is located in the industrial region of Edmonton called Rosedale. The site location created the challenge of limited transit connectivity for occupants. Bicycles are one viable alternative for single occupant vehicle use. The project encourages cycling by providing showers for occupants, and storage for bicycles, 18 outdoor bike racks in total with 6 that are sheltered and secured for dedicated staff use. There is a keyable locking door for the bike parking enclosure, and the enclosure is located within the secure zone of the facility, with exterior 24/7 security camera monitoring. In addition to security of bicycles, there are also lockers for storage of helmets and cycling clothes.
Dark Skies
The more projects incorporating light pollution reduction measures in their design in a region, the darker the night sky will be, providing ecosystem and urban community benefits. The Rosedale Letter Carrier Depot utilized full cut-off exterior light fixtures on all pole-mounted site lighting and building mounted Metal Halide luminaries are full cut-off and dark sky compliant. All pole-mounted luminaries near the property line were specified with spill lighting eliminators to reduce light trespass on adjacent properties. Exterior lighting is connected to the building via a low voltage lighting control system and controlled automatically through a timeclock and photocell. All interior lighting is controlled by time clock which turns off all lights and/or switches to night lighting during non business hours.
Heat Island Effect Reduction
As part of the project’s programming, a fleet of 110 mail vehicles use the distribution facility. This creates a large demand for hardscape space outside the building. In order to compensate for the need for extensive hardscaping on site, large shade trees were planted to create shade over the parking areas. This effort also reduces heat island effect and minimizes impacts on microclimates. Trees planted included Colorado Spruce, Toba Hawthorn, and Prairie Spire Green Ash. To conserve moisture and prevent evaporative water loss from the soil surface, a mulch was applied to the tree beds.
Water
Conserving water and water quality is a considerable issue in Alberta. Using low flow fixtures, the Letter Carrier Depot saves nearly 41% of potable water compared to the same type of project with conventional fixtures.
As a semi-arid climate, the landscape selected for this project did not require permanent irrigation. As a result, irrigation systems were not installed for this project, both creating monetary and water savings. Hardy drought tolerant plants were selected, including Siberian Dogwood, Wolf Willow, Scandia Juniper, Blue Tam Juniper, Karl Foerser Feather Reed Grass and Blue Fescue.
Energy Conservation Measures
Projects obviously need to be heated and ventilated to optimize occupant comfort, but there must be a balance between energy for HVAC and energy savings. Numerous strategies can be adopted on even the simplest of buildings for energy savings.
High Performance Envelope
Throughout the design process, the owner-operator of the building was looking for solutions with reduced life cycle costs. One significant, but largely invisible, way for this project to do this was through insulation. This project incorporated a highly insulated and sealed envelope (average Rsi=4.4 W/m2K and a high thermal performance glazing system (U=1.59 W/m2K). The project’s thermal mass is also used to stabilize indoor comfort conditions.
The result of this high performance envelope is reduced heat losses in winter and solar gain in summer. The envelope greatly contributed to the 31.8% energy cost savings achieved by this project (as compared to its ASHRAE 90.1-2007 baseline).
Air Curtains
A large challenge with this project was the potential for significant heat loss due to the need for frequent and extended access to the outdoors. To address this and prevent considerable heat loss through the large openings at the loading docks, electric air curtains were incorporated, which cut down on outdoor air infiltration.
Heat Recovery Ventilation
Additional building systems that provided energy savings was heat recovery ventilation. Rooftop heat recovery ventilation (HRV) units mix recovered waste heat from exhaust systems with fresh outdoor air and then deliver this newly conditioned air to regularly occupied spaces. To further ensure that indoor air is healthy, carbon dioxide sensors monitor indoor air quality in the space and notify the building operator when CO2 levels are beyond acceptable thresholds.
Lighting can be a great contributor to overall energy conservation measures and reduced energy loads. High-efficiency fluorescents, compact fluorescents and LEDs were specified to reduce total lighting power density. Lighting controls also add to energy efficiencies, through low-voltage systems and savings through lighting scheduling.
Green Power
The owner-operated has opted to invest 70% of the electricity value required to operate the building for the next two years in certified green power sources, through the purchase of green power certificates. This is done to mitigate the impact of greenhouse gas emissions associated with the project, as well to support the proliferation of renewable energy.
Materials and Resources
Major components of the project’s structure arrived to the site from within 800km of where they were extracted and manufactured to reduce the impact of their transport carbon footprint, which also supports local business. Likewise, materials have been selected and incorporated with special attention paid to their post-consumer and post-industrial recycled content. As a means to show support and invest in sustainably managed forests, over half of the wood used in this project was sourced from certified Forest Stewardship Council (FSC) forests.
Construction Measures
Measures put in place during construction demonstrated a commitment to green construction management. Over 85% of construction waste was diverted from conventional landfill to recycling and salvage streams. Considerable effort was directed towards issues of indoor environmental quality and health during construction through the implementation of an indoor air quality management plan.