Canada Post Corporation St. Albert Letter Carrier Depot
Certifications & Awards
- LEED Canada for New Construction and Major Renovations (registered)
Project Team
- LEED Consulting: Light House and Omicron
- Building Science Professional : Omicron
- Contractor: Synergy Projects Ltd.
- Landscape Architecture : Matrix Landscape Architecture
- Civil : McElhanney Consulting Services Ltd.
- Electrical : Omicron
- Mechanical : Omicron
- Architect: Omicron
- Owner : Canada Post Corporation
Green Building Audio
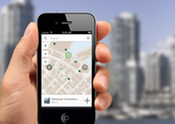
Our audio tours qualify.
Get one today!
Canada Post St. Albert Letter Carrier Depot - Joanne Sawatzky, Light House
Summary
Located in Campbell Business Park North in St. Albert, Alberta, this Canada Post project is a one-storey, 1,672 square metre (18,000 square feet) light industrial warehouse building containing the operations, administrative and support areas for the sorting and consolidation of large quantities of mail.
Conventional construction and building systems were used throughout the facility in accordance with the prototypical building design and owner’s functional requirements. This new facility needed to respond to future uses and changes in the postal system as well as current programming demands. A durability plan was included to meet these future needs. The use of a prototypical design for all new Letter Carrier Depot facilities has allowed Canada Post to produce a repeatable, cost-effective and efficient light industrial building to meet the needs of its staff and users.
The building includes workspace for 33 full time equivalent employees and 13 transient occupants from the Canada Post fleet. The facility is mainly an office/warehouse with ancillary spaces such as locker room, showers and lunchrooms.
Integrated Project Delivery
Integrated Project Delivery (IPD), also know as Integrated Design Process (IDP) is an alternative method for project delivery that is increasingly being used within the development, design and construction community. It is especially relevant to high-performance buildings as it seeks to maximize potential synergies and efficiency of projects. IPD is characterized by increasing the design and pre-construction effort and exploration during the early stages of a project, when opportunities to influence sustainability and operational efficiency are greatest and least expensive to implement. In contrast to the traditional delivery models, IPD is non-linear, requiring iterative study of design options at all levels of detail, and frequent collaboration amongst owners, project managers, and architectural, engineering, interior design and construction disciplines.
An Integrated Project Delivery approach was employed on St. Albert Letter Carrier Depot to capitalize on project efficiencies gained through early participation of all disciplines, including estimating and pre-construction services, during schematic design and design development. The specific green building strategies for this project were selected to minimize anything additional costs to the projects compared to the baseline prototypical building. Particular emphasis has also been placed on minimizing long-term operational costs and improving the quality of the indoor environment.
Sustainable Sites
As a distribution facility, the St. Albert Letter Carrier Facility has 31-vehicle fleet for mail distribution. To meet the large space demands for this fleet moving on and off site, there was a challenge in delivering sufficient green space. The project compensated for this by offsetting hardscape areas with a large number of tree plantings in the parking areas. A secure area for bicycle storage as well as place to change provides staff with facilities that encourage cycling as a viable form of commuting.
Landscaping on site was adapted to meet both The City of St Albert and LEED requirements to be drought-tolerant. To save on potable water use, these plantings will not require irrigation after a two-year establishment period. The civil engineer designed a controlled system for on-site rain water management to minimize impacts to the local watershed.
Light pollution is a problem that can be easily addressed through a conscious electrical design. The design team worked to ensure that light trespass from the building and site lighting is minimized to help contribute to a dark night sky.
Water Efficiency
With consideration to the fact that water efficiency is a regional priority for urban areas in Alberta, the project team reduced indoor water usage by 41 percent. Low flow fixtures were installed and no outdoor potable water will be used for the landscaping after a two-year establishment period.
Water closets are two-piece dual flush wall mounted type, using 3/6 L of water per flush. Urinals are ultra-low flow (0.5 L per flush) type. Lavatories in washrooms have hard wired, automatic infra-red low flow faucets (1.9 lpm). Showers use low flow shower heads (7.6 lpm), with pressure and temperature balanced, single lever shower valves. The use of these highly efficient plumbing fixtures reduced long-term operational costs.
Energy Conservation Measures
Reduced energy consumption was accomplished primarily through incorporating passive design principles. By using high performance building envelope assemblies and glazing with low-e double-glazed windows, the envelope reduces heat loss in winter and prevents solar heat gain in summer.
Other energy conservation measures on this project include the installation of a heat recovery system, demand controlled ventilation and efficient lighting design. The proposed design resulted in 31% regulated energy cost savings as per ASHRAE 90.1-2007, which is equal to 10 LEED points under LEED credit EAc1.
Enhanced commissioning ensured that the building was designed, constructed and operates in accordance with owner requirements. The goal of commissioning is to ensure that the all the systems’ targeted efficiencies run as designed. The resulting design will deliver significant operational cost reductions over the life of the building.
The heating system in the sorting area consists of two high-efficiency packaged roof top units providing both ventilation air, heating and cooling to the warehouse space. Supplemental heat is provided by ceiling mounted gas fired unit heaters. Electric air curtains are installed at the loading dock doors to cut down on outdoor air infiltration. The administration area heating system consists of a single-zone packaged roof top unit with electric baseboard heating along the perimeter of the building.
All cooling in the building is through three high efficiency packaged roof top air conditioning units. These units provide adequate cooling for both the office and warehouse spaces. The units were designed to utilize non-ozone depleting refrigerants, humidification, free cooling economizer, exhaust heat recovery and MERV 14 filters.
Ventilation air to the space is provided by the packaged rooftop units, with ventilation rates delivered in accordance with ASHRAE 62.1 - 2007 standard for minimum acceptable indoor air quality performance. Carbon dioxide (CO2) sensors monitor indoor air quality in the space and alarm the building operator when PPM levels are beyond acceptable thresholds. The building systems are controlled and monitored by a building automation system (BAS), which is tied to all major mechanical equipment as well as the lighting and power systems. This allows for complex system control and scheduling as well as off site monitoring. The BAS system also monitors utility consumption through a series of building meters in an effort to measure and verify overall building performance.
Materials and Resources
The building utilizes conventional steel frame construction (columns, beams and joists) with two distinct exterior cladding systems: a metal insulated panel wall assembly on the warehouse exterior and prefinished Glass fiber reinforced concrete panel on a conventional light steel stud infill framing system for the administration area facade and building entrance. Exterior canopies are provided around the building to enhance the aesthetic appeal and provide some shelter for staff movement and access around the building. Interior development includes conventional steel stud partitions, steel doors and frames, and functionally-driven interior finishes including vinyl composite tile, exposed ceiling and acoustic ceiling panels, paint and millwork.
To meet the requirements for achieving Recycled Content and Regional Materials in the project, the major components of the structure arrived at the project site from within 800km of where they were extracted, manufactured and produced. Materials have been selected with special attention paid to both post-consumer and post-industrial recycled content. FSC-certified wood was incorporated where possible.
The percentage of diverted waste generated on-site from construction material, packaging or general waste was 76%, and the elimination of waste was prioritized through use of pre-manufactured materials and systems.
Indoor Environmental Quality
Considerable effort was directed towards the issues of indoor environmental quality and health during construction as well as post-construction through the implementation of an indoor air quality management plan. All paints and wet products employed during construction met the VOC limits requirements, as well as the flooring systems and composite wood products, for improved occupant health.