UW North Campus Phase I - LTC & RIA - The Village at University Gates
Certifications & Awards
- LEED Canada for New Construction and Major Renovations (registered)
Project Team
- Contractor: Van-Del Contracting Ltd.
- Landscape Architect: Ron Koudys Landscape Architects
- Commissioning Consultant: Zon Engineering / RFB Commissioning
- LEED® / Energy consultant: Zon Engineering Inc.
- Site Services: Stantec Inc.
- Structural Engineer: Gray & Fick Ltd.
- Mechanical / Electrical Engineer: MNE Engineering Inc.
- Architect: Cornerstone Architecture Inc.
- Owner / Developer: Schlegel Villages Inc.
Green Building Audio
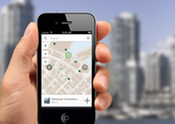
Our audio tours qualify.
Get one today!
Village at University Gates - Richard Hammond of Cornerstone Architecture and Brad Schlegel of Schlegel Villages
Summary
This is the first phase of a continuum of care community for seniors developed by Schlegel Villages in conjunction with the University of Waterloo. Phase I consists of a 192-bed Long Term Care Facility connected with a Research Institute for Aging.
The University of Waterloo, Conestoga College and Schlegel Villages have partnered to develop a continuum of care community, complete with a centre of excellence for research, training and innovation in senior health care and wellness.
Located at the University of Waterloo’s North Campus, the Village at University Gates, the first of the three phases is a 192-bed long-term care home, coupled with the Schlegel-UW Research Institute for Aging (RIA). Constructed in August 2015, the purpose of the RIA is to improve the quality of life for older adults through partnerships in research, education and practice. The goal of the project is to prepare for Canada’s aging population amidst “a living classroom and a living research environment.” Research teams investigate the role of nutrition, geriatric medicine and spirituality in the quality of life for seniors, and students will receive first-hand experience for their careers.
The two later phases of the project include a senior’s assisted and independent living development and a primary care health centre to create a full continuum of care.
The Long Term Care (LTC) Facility is a three-storey project connected to the Schlegel-UW Research Institute for Aging (RIA). Situated on a 3.67 hectare site, the project contains roughly 11,500 m2 of day program areas, family rooms, therapy and resident rooms. The connected Research Institute for Aging facility is approximately 2,800 m2, consisting of offices, classrooms, examination rooms and laboratories.
The project is targeting a Gold level of LEED Certification as defined by the Leadership in Energy and Environmental Design Canada for New Construction 2009 (LEED® Canada-NC 2009) green building rating system.
Project Highlights
- Interior water fixtures save over 5.2 million litres of water a year
- 136 kW DC Photovoltaic (PV) solar panel system for on-site renewable energy equal to 6.5% of the project’s energy needs
- Energy cost savings of 41% compared to Model National Energy Code for Buildings (MNECB) reference building
- Half of all wood products installed (by value) support sustainable forestry practices through Forest Stewardship Council (FSC) certification
- Safeguarding of Indoor Air Quality through adherence of VOC limits, pre-occupancy IAQ testing and green housekeeping and exterior maintenance plans
Sustainable Sites
Amenity rich
The project site is located on the west side of the University of Waterloo’s North Campus, which is a short walk to the neighbouring residential community, nearby amenities, such as cafes, parks, and the adjacent Laurel Creek Reservoir.
A project that provides walkable access to a variety of nearby amenities provides an ease of use, and a reduction in the need for vehicular use, which enhances residential quality of life. Nearby amenities can also facilitate an independent lifestyle for seniors.
Green Transportation
In the interest of providing options for green transportation to reduce reliance on single occupancy vehicle use, the project site is closely located to frequent bus service, with stops along Fisher-Hallman, Bearinger Road and Laurelwood Drive. For additional connectivity to the University of Waterloo, the facility provides a shuttle bus throughout the day to reduce the need for students and staff to drive to the Schlegel-UW Research Institute for Aging.
In the parking area, six electric vehicle charging stations have been installed to encourage the adoption of low-emitting vehicles. Installing electric vehicle charging stations is a prime means of future proofing a parking area. Designated carpool parking spaces have also been provided to encourage occupants to carpool to the facility.
Green space
The Village at University Gates facility ensured there was open space equal to the building footprint available for occupants to enjoy, even after future development phases were taken into account. The site was graded to allow direct access to gardens on the main floor for residents as well as for the central rehabilitation program participants. Each home area on the upper floors is provided with a large balcony. In addition to the open outdoor space, a large covered porch area is provided on the main floor adjacent to the front entrance, with accessible walkways to outdoor spaces.
Rain water management
With the development of a site comes an obvious increase in the impermeability of a site. The way rainwater will travel on and off the site is an important design consideration. Municipal storm drains are taxed whenever there is a significant storm event, making storm water management a key environmental priority within the region. Rainwater falling on the site is managed as part of a larger development, which is governed by the University of Waterloo North Campus Master Plan. A large detention pond was constructed just off-site to manage the majority of the rainwater from the total development. The pond controls the discharge into the adjoining Laurel Creek Reservoir.
Cool roof
To address the local environmental priority heat island prevention in urban areas, the project’s roofing system consists primarily of a Thermoplastic Polyolefin (TPO) roofing membrane. Installing this form of light-coloured or ‘cool’ roof, creates a reflective surface whereby sunlight bounces off the surface to prevent solar heat gain. The heat gain from solar exposure on a building can contribute to a number of negative and inefficient conditions such as extreme temperature fluctuations of roofing materials, leading to premature wearing of the roofing system. Solar heat gain on a roof can also increase the cooling load of a project interior, contributing to summertime peak energy demand, space conditioning costs and greenhouse gas emissions. Finally, the heated roof surface can lead to heat island effect, where built-up areas have hotter temperatures, which can create negative habitat effects for flora and fauna.
Dark sky friendly design
Additional habitat considerations on-site pertain to project lighting. Light pollution is caused by excessive artificial light that can brighten the night sky, which can negatively affect wildlife like migrating birds, as well as human circadian rhythms and our general enjoyment of a natural dark sky. To guard against light trespass off the site, the Long Term Care Facility has been designed to use ‘full cutoff’ exterior fixtures in parking and driveway areas, with lighting controls in the residential suites and common areas to reduce interior lighting by 50%.
Water Efficiency
Canadians are some of the highest per capita users of potable water in the world. Each building project reaching for LEED certification has the opportunity to incorporate water use reduction through design.
For instance, to reduce the need for potable water needed for irrigation, the landscape design incorporated principles of xeriscaping. Careful selection of drought-tolerant native and adaptive plant species reduced the need for irrigation. In addition, the project installed a 40 m3 rainwater cistern on-site and connected it to the irrigation system. Consequently, there is zero potable water used for irrigation on this project, and the system will run dry if the cistern is empty. Inside the building, potable water use was reduced by over 45% through the specification and installation of low-flow fixtures. The average flush rates for toilets and flow rates for faucets are as follows:
Toilets: 4.86 Litres Per Flush (LPF)
Urinals: 0.5 LPF
Lavatory Faucets: 1.9 Litres Per Minute (LPM)
Showers: 5.7 LPM Kitchen
Sinks: 1.9 LPM
Through these measures, the project modeled a total annual savings of over 5.2 million litres of water annually, a total reduction of 46% compared to standard water consuming fixtures.
Energy and Atmosphere
The project had high aims for energy conservation. Starting with thermal performance, the project sought to build a well-insulated envelope with high insulation values and good windows. The R-Value of the building roof is approximately 59% higher than what a base building design would be. Windows were selected with a high thermal performance, with U-Values that provide an approximately 35% lower coefficient of heat transfer than the baseline building design.
From there, the project team prioritized energy conservation measures in efficient mechanical design and equipment. The fans in the air-handling units are equipped with variable-speed drives to save more energy compared to fixed or constant speed drives. The energy from the air-handling units is also maximized with heat recovery heat wheels on the exhaust air.
Efficient condensing boilers were used for the heating plant, which have much lower fuel and running costs than conventional boilers. Condensing boilers recover as much waste heat as possible using a large and efficient heat exchanger.
Renewable energy
Once a project has found every reasonable energy conservation measure, further energy savings can be boosted with the use of an onsite renewable energy system to take advantage of the sun’s energy. A 136 kW DC Photovoltaic (PV) system was installed on the roof of the Long Term Care portion of the building. These solar panels produce about 153,357 kWh of electricity, which is the approximate equivalent of 6.5% of the total electricity consumption on-site.
The sum of these energy conservation and renewable energy production measures resulted in the proposed building model showing an energy cost savings of 41%, as compared to the Model National Energy Code for Buildings (MNECB) reference building.
Materials and Resources
The LEED rating system works as an industry lever to encourage teams to implement design and construction practices that are more resource efficient for a lower environmental impact and higher performance. Construction practices are making gains towards greater coordination of construction waste whereby recyclable materials are separated to divert as much tonnage from the landfill as possible.
Reducing construction waste
This project created construction waste management practices that resulted in a 76% diversion of waste from landfills. When it comes to LEED and building materials, the rating system has been key in the prioritization of lower impact materials, and in encouraging manufacturers to satisfy the demand for these products. Prioritizing the use of recycled building products creates an opportunity for projects to conserve natural resources and reduce the use of virgin and/or non-renewable materials.
The project made every effort to specify and install recycled building materials wherever practicable. Recycled materials that could be readily sourced with minimal to no incremental cost were identified early in the project, such as cast-in-place concrete and concrete block, asphalt, rebar and miscellaneous steel products, insulation, composite wood products, gypsum, and acoustic ceiling tile.
The project also sought building materials that were manufactured or extracted within the region. The criteria for a product to be considered regional are for materials to arrive from no further than 800 km away if freight-shipped or 3 times the distance if shipped by rail or water.
Certified wood
The project team worked towards sourcing and installing Forest Stewardship Certified wood on at least half of all wood products used on-site, with a push to source as much FSC content as possible.
Indoor Environmental Quality
There are a number of factors that contribute to the indoor environmental quality of a interior space, including lighting, air quality, acoustic conditions and occupant control over lighting and thermal conditions. The design team incorporated a number of measures to address these needs.
The building’s lighting and thermal controls were designed to provide occupants with a high level of personal control. There are thermostats in each suite and over-bed lighting for each resident, combined with task lighting in offices and workstations, and multi-scene lighting controls in the shared (multi-occupant) spaces. In total, there are individual lighting controls for over 90% of building occupants, and all shared spaces comply with industry standards (ASHRAE 90.1-2007) for group control.
Not only does the provision of autonomous over automated controls give occupants the ability to change their settings to suit their comfort, it can also improve their perceived level of comfort.
In an effort to enhance occupant thermal comfort in all residential and shared spaces, at least one operable window or thermostat control is provided for half the building occupants, at a minimum, in their resident suites and offices, as well as all shared occupant spaces.
Source-Control methods for Air Quality
Regarding the air quality of the indoor spaces, the project made a number of commitments and plans to prevent and reduce indoor contaminants and pollutants. It was essential for this facility to protect indoor air quality, especially for its vulnerable building occupants. For this reason, products were carefully specified to comply with limits of Volatile Organic Compounds (VOCs), which are chemical gases, such as formaldehyde, that are released into the air from certain building materials. This effort was successfully implemented by ensuring VOC limits were included in construction documents so construction team could select products of compliance, many of which are readily available due to market demand.
IAQ Testing
The project interior underwent indoor air quality testing prior to residents moving into the building to ensure that the construction activities did not compromise the air quality, and to confirm that the particulate and emission rates were below the maximum allowable industry rates. It was equally imperative to ensure that the same diligent care taken to protect indoor air quality during construction would carry on throughout the building’s operation.
One of the most effective ways to reduce the amount of chemicals released into a building, aside from banning tobacco smoke (which is the law), is to create a toxic-free cleaning regimen and purchasing policy.
A green cleaning program was developed and executed, which conforms to the standards prescribed in the LEED for Existing Buildings: Operation and Maintenance (EB:OM) rating system.
The client also committed to a low-impact building exterior and hardscape management program, also in line with LEED EB:OM requirements.
This plan focuses on a source control-style reduction of chemicals used for hardscape and exterior building maintenance and formalizes procedures in the interest of reducing water and energy use for these activities.
Low-mercury lighting
To reduce the amount of mercury within the on-site fluorescent lighting fixtures, a minimum of ninety percent of all interior and exterior lighting fixtures were specified to contain no more than 90 picograms of mercury per lumen-hour, which is a standard upheld by the LEED EB:OM rating system. This standard is now part of the operations plan to ensure that low mercury fluorescent lamps are used in all interior fixtures for the life of the building.